THE IMPACT OF AUTOMATION ON LOGISTICS REAL ESTATE
November 4, 2021
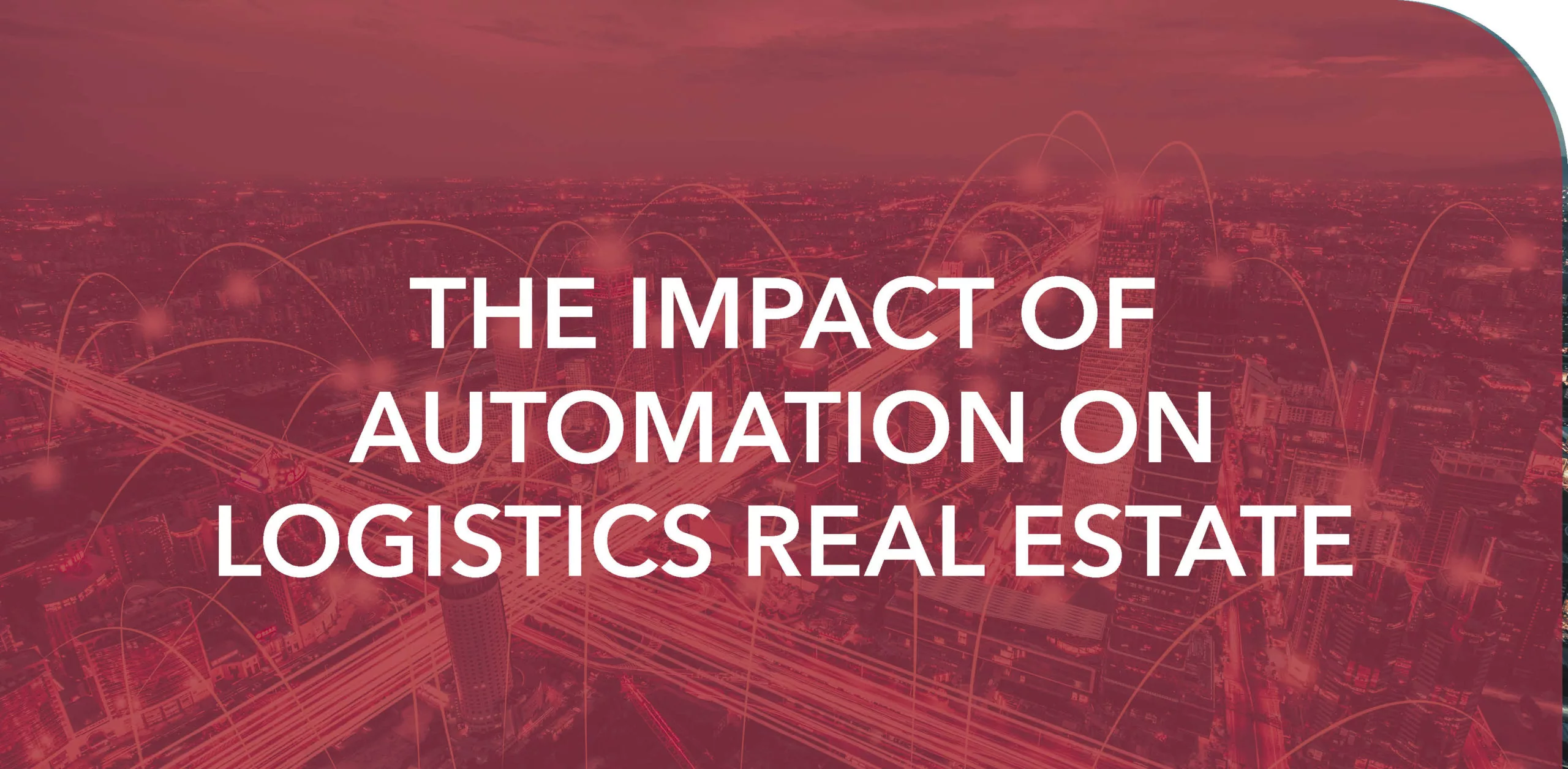
The Impact of Automation on Logistics Real Estate
Third-party logistics and transportation companies continue to experience and observe the transformation that explosive e-commerce demand has had on their business and on the broader economy. Facilitating growth while managing risks have become top priorities, while shortages at every step along the way pose challenges to timing and execution.
Most firms are familiar with the situation surrounding labour and raw materials, which have translated into internal operational issues. However, this same lack of inputs is wreaking havoc on the industrial market, especially in the Greater Toronto Area.
The GTA, as of Q3 2021, continues its tightening, with a 1.1% overall vacancy rate, rents rising to an average of $13.18 PSF Net, and a 12-month net absorption of over 10M square feet; compared to less than 6M square feet of new deliveries year-to-date.
As mentioned, supply chain issues are constraining the pipeline of new construction, pushing up rents, and making both growth and risk management difficult to achieve. With that in mind, many 3PLs have turned to technology to help manage their existing space, while patiently waiting for opportunities to lease, pre-lease, acquire, or develop.
Today, we’ll explore how automation and other technologies are aiding logistics firms in these unprecedented times.
The Role of Technology in Logistics Real Estate
1. Stretching the Bandwidth of Existing Operations
According to a report by 3PL Central, “85% of 3PL warehouses experienced growth this year, with 23% reporting growth of more than 50%.” Given the all-time low vacancies and difficulty expanding, embracing technology has become vital to those already operating at or near full-capacity.
2. Compensating of Labour Shortages
The aforementioned study also found that around 50% of 3PLs are struggling to find and retain qualified workers while also experiencing significantly inflated wages. This supply trap means warehouse management systems will be needed to bridge the gap, especially as we approach another peak season this winter.
3. Mitigating Future Risks
The theme of the past 18 months has been about building resilient supply chains. A core aspect of this philosophy is producing flexibility – both ways. Whether demand subsides, retailers stockpile inventory further, or companies revert to just-in-time (JIT) models, having the ability to turn on a dime will prove advantageous.
4. Tapping into Cubic Volumes
In response to land and warehousing shortages, developers and users alike are constructing state-of-the-art facilities with higher and higher clear heights. While extremely efficient, these buildings require racking, equipment, and warehouse management systems in order to safely and quickly pick, pack, and move inventory.
5. Winning Market Share
E-Commerce continues to grow its share of retail sales while other industry sectors, such as grocery delivery and life sciences, are just beginning their upwards trajectories. Over 53% of 3PLs respondents stated they fulfill orders in less than 90 minutes after receipt – a metric closely linked with annual order volume growth. Sustaining this level of performance will only become more difficult with scale and as the supply-demand imbalance increases.
Summary
The logistics sector has been forced to adapt in real-time as global events compress forecasted growth from one or two decades into a matter of years. As other industries follow e-commerce’s lead, we expect demand to push forward, albeit in an environment where much of the previously existing excess in supply has already been absorbed.
This new equilibrium will create challenges in securing and managing your industrial logistics space, and will further emphasize the need for technology and automation, coupled with strategic real estate moves.
On that note, if you would like our team to assist with your next lease or purchase, or for more market intel or off-market opportunities, please contact us directly.